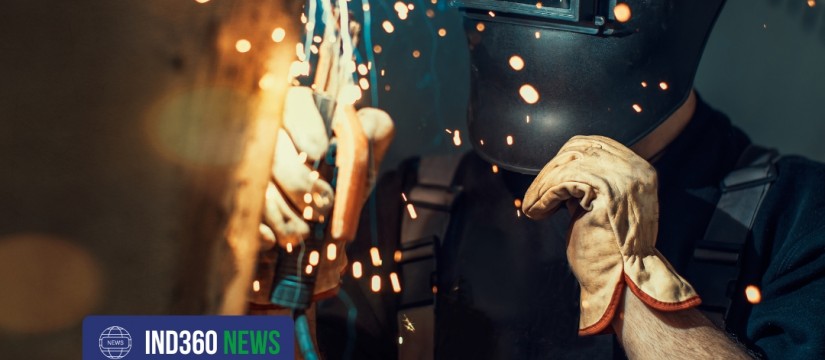
A soldagem a arco, essa jovem senhora de mais de 100 anos de idade, sempre foi considerada uma mistura de ciência e habilidade. Com a chegada do século XXI e seus requisitos de alta performance, produtividade e geração de produtos em escala nunca vista, tal processo passou a requerer, nos dias de hoje, atenção redobrada no atendimento a várias áreas do conhecimento, de forma a produzir equipamentos soldados com baixo custo, elevadíssima qualidade, garantia de performance prolongada e demais requisitos similares.
Confira na integra artigo escrito por nosso diretor, o Eng. Fernando Lescovar especialmente para o Portal Ind360 , Ind360 , que é uma plataforma de marketing digital com foco na indústria e busca alcançar profissionais, engenheiros e compradores e temos o objetivo de auxiliar a atrair, converter e reter clientes no setor industrial.
Introdução:
Baseado, portanto, nestes fortes requisitos atuais, vamos tratar nos parágrafos seguintes de 6 grandes erros que normalmente são cometidos por empresas que produzem itens soldados e que poderiam obter maior lucratividade e controle de processo ao identificar um ou mais desses erros em seu dia a dia e corrigi-los.
1. Não pensar na qualidade de forma objetiva
A qualidade requerida para um conjunto soldado (equipamentos, estruturas, etc) depende fortemente da norma construtiva que dá suporte a esse equipamento, legislação local, assim como também depende dos requisitos suplementares determinados pelo cliente.
Assim sendo, a aplicação dos conceitos de qualidade está diretamente associada aos critérios de aceitação e às descontinuidades definidas para o produto.
Um erro comum é estabelecer a qualidade absoluta de uma junta soldada como requisito a ser atendido, ou esquecer de olhar para os requisitos do pedido e aplicar o padrão da empresa fabricante. Estes erros são fonte de grande retrabalho ou desperdício de recursos.
A qualidade, portanto, é a adequação pura e simplesmente do padrão previamente determinado e desejado pelo cliente e pelos organismos oficiais responsáveis pelas normas de qualidade vigentes.
Conhecer tais requisitos, legislações e normas pode gerar a otimização de recursos em face a não haver desperdícios ligados a excesso de testes e inspeções, nem ausência equivocada de inspeções.
2. Não pensar em fabricação enxuta
A fabricação enxuta ou lean manufacturing é baseada no método Toyota de fabricação e possui inúmeras ferramentas que ainda não foram absorvidas por grande parte do mercado industrial brasileiro que produz equipamentos soldados, principalmente na indústria de base. A produção enxuta, quando colocada em uso, pode agregar ganhos expressivos de produtividade, redução de tempo, desperdícios e retrabalhos, posicionando assim, portanto, a atividade de soldagem como um processo de fácil elevação da lucratividade geral da fábrica.
Alguns exemplos de ferramentas da manufatura enxuta são:
- Kaizen
- Kanban
- Mapa de fluxo de Valor
- Just in time
- 5S
- Jidoka e Poka Yoke
3. Não se cercar de ferramentas de trabalho práticas
Formas de trabalho antigas que consideravam cálculos de volume de consumíveis, pesquisas de listas de EPSs qualificadas, controle de soldadores, feitos a mão, de forma a gerar grande consumo de tempo dos profissionais, hoje já são plenamente possíveis de serem mecanizadas por meio de aplicativos dedicados a cada uma dessas funções, integrados aos dados disponíveis na empresa.
O uso dessas ferramentas permite treinamento rápido de profissionais ainda em treinamento (learn on the job) e a disponibilização de profissionais de maior conhecimento para atividades mais nobres, que requeiram forte dedicação e entendimento.
Veja nossa solução ao final desse artigo!
4. Não dominar os conhecimentos da engenharia de soldagem
O desenvolvimento de aços de composição química e metalurgia mais delicadas e complexas bem como a evolução dos processos e maquinas de solda requerem o conhecimento de itens de engenharia de soldagem, tais como, controles finos de aporte térmico, metalurgia da soldagem e seus diversos aspectos, tais como, composição do metal de solda, característica metalúrgica da zona termicamente afetada, dureza resultante nos diversos segmentos da solda e assim por diante. O desconhecimento desses conceitos conduz a juntas soldadas que eventualmente podem ser susceptíveis à fadiga precoce, bem como surgimento de trincas e desgastes inesperados ao longo do seu uso.
5. Não executar a soldagem de forma segura
A atividade de soldagem é considerada uma atividade à quente que pode, como consequência, gerar a ignição de fluidos inflamáveis, incêndio de materiais combustíveis, gerando, portanto, altos riscos à na equipe que esteja próxima da execução desse processo.
Além desse aspecto específico, a soldagem a arco é fonte geradora de radiação infravermelha e ultravioleta, gerando assim também consequências relacionadas aos aspectos negativos desses tipos de radiação.
Outros riscos ligados a soldagem se situam no campo da geração de gases resultantes da fusão dos consumíveis e dos riscos de choques elétricos. Essas preocupações, associadas ao uso de equipamentos de proteção individuais e coletivos, se fazem essenciais para a correta produção de soldagem em ambiente seguro.
6. Não se manter constantemente atualizado e treinado
Maquinas de solda, dispositivos complementares e acessórios são modernizados constantemente.
Normas são revisadas e publicadas a cada dois anos, novas descobertas sobre técnicas, processos e consumíveis são lançadas no mercado, temas como internet das coisas (IoT), armazenamento na nuvem, big data e robotização de nova geração são ferramentas também da indústria 4.0 que evoluem rapidamente mês a mês. É, portanto, item obrigatório do profissional de soldagem buscar ambientes de formação e treinamento, assim como manter a sua conexão com a comunidade de solda para que não se cometa o erro de se transformar em um profissional ultrapassado em pouco tempo.
Este aspecto também abrange o time de fábrica, incluindo soldadores, encarregados e demais profissionais que merecem atualizações e treinamentos de melhoria contínua.
O Grupo Technik tem condições de auxiliá-lo em todas as situações apresentadas neste texto. Conte conosco.
Sobre o Grupo Technik
O Grupo Technik tem a missão de gerar valor trazendo inovações e ferramentas que facilitarão a gestão e engenharia das indústrias em geral, frente aos desafios no século XXI.
Tem o propósito de colaborar e ter participação efetiva nas mudanças e adaptações as quais o setor industrial brasileiro está sujeito
Fernando Lescovar Neto 19.9 7169 5770
Alguns motivos pelos quais você precisa automatizar a localização de EPSs e CQSs
Ao longo de nossa trajetória trilhada junto a nossos variados clientes, por muitas vezes discuti o gerenciamento de documentos de soldagem, como Registros de Qualificação de Procedimentos (RQPS), Especificações de Procedimentos de Soldagem (EPS) e Certificados de Soldador CQS).
O que mais se observa é o seguinte:
Quando chega um novo projeto para orçamento, eles entregam o projeto a seu analista sênior de soldagem e ele busca, junta por junta, em uma tabela os soldadores e eps qualificados, o atendimento a todas as variáveis essências do projeto (espessura, posição, família de materiais, tratamento térmico, processos, cobre juntas, etc). O custo dessa atividade é muito alto, pelo tempo dedicado, e envolve altos riscos ligados a erros, pois todos somos humanos.
Veja a seguir:
1. Ao qualificar um RQPS redundante (ou seja, já o tinha qualificado, mas devido a um erro no processo de verificação, volta a qualificá-lo e que custa ~ R$3000,00, não contabilizando o tempo perdido, o salário do soldador, e custos de materiais), há perda (desperdício) de recursos.
Ainda neste caso, qualificando-se um soldador redundante, que custa até R$500,00, acrescenta-se este custo também ao custo anterior.
2. Por outro lado, ao se equivocar por não identificar falta de EPS para as juntas em fabricação, por vezes pode-se ter clientes exigindo que você pare todo o trabalho até que se faça a nova e urgente qualificação.
Isso não é tão fácil de quantificar em termos de prejuízo, porque depende do projeto e do tamanho da empresa, mas pode-se chegar a centenas de milhares de Reais
E por que isso é um problema comum?
Pelo fator humano. Não importa quão bom seja um engenheiro ou analista, ele ainda é apenas humano, e fazer muitas verificações cruzadas de informações o cansará e poderá eventualmente causar alguns erros, o que poderia fazê-lo sinalizar uma solda específica como não qualificada (quando, na realidade, é), ou pior, fazendo-o sinalizar uma solda específica como sendo qualificada (quando não é).
Ambos irão aumentar o custo para a empresa e a sua dor de cabeça também.
Como você pode evitar isso completamente?
Você deve trabalhar para ter um banco de dados preenchido de todos os seus Registros de Qualificação de Procedimento (RQPS), Especificações de Procedimento de Soldagem (EPS) e Certificados de Soldador (CQS), com todas as variáveis essenciais que são relevantes para os códigos com os quais você trabalha. A partir daí fazer uso do aplicativo Technik para seleção e controle de documentos de solda.
Quer saber mais? Clique aqui e consulte o Grupo Technik Engenharia!